- Full Time
- Chennai, Tamil Nadu, India
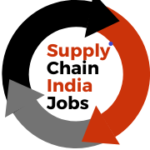
Husky Technologies
Supplier Quality Analyst-Husky(India)Chennai
Location : Chennai, Tamil Nadu, India
Job Description
Husky TechnologiesTM has a strong foundation built on innovation, close customer relationships and a unique culture and values. We are dedicated to offering our customers the highest quality products and services and are looking for people with the inspiration and talent to develop with us as we pursue our ambitious growth strategy. We are a leader in developing state-of-the-art technology and it is this technology base that uniquely positions us to serve customers who seek differentiation through solutions that provide speed, flexibility and maximum productivity. This capability is at the core of our mission and competitive strategy.
Husky TechnologiesTM offers a wealth of opportunity for personal growth and development. Most importantly, Husky Technologies TM offers an opportunity to work with – and be challenged by – a team of great people. Our success is possible because of the creativity, intelligence and passion of our people around the world and their desire to lead change. At the same time, we are not afraid to expect a lot and strive for leadership in all of our key markets. We are a company taking on new challenges and for the right people this means exceptional career development opportunities, the chance to be part of a team that is the best in the world at what we do and the experience that comes from working in an environment that demands constant transformation and innovation.
Husky TechnologiesTM is an exciting company with tremendous potential. We have a great team and great expectations. If you are attracted to bold goals, believe in uncompromising honesty, support mutual respect, care about environmental responsibility, have a passion for excellence and a desire to make a positive contribution – then we want you to join the Husky TechnologiesTM team!
- Supplier Support Specialist for Global Spare parts Operations
- Clearly define the issue details (Customer complaint and / or Internal Quality issues) for supplier parts (Internal and External) and document data for potential escalation
- First Aid – Own the fast replacement/rework / modification to supplied components to minimize affected sales order / Mod & Upgrade Project Shipment / execution
- WIP check containment for upstream projects & supplier stock – Communicate and ensure that Containment is completed, and stock is clear; Get a clean date.
- Work closely with suppliers and Lane SQE (as needed) for effective Root Cause analysis and define the corrective actions with clear timelines
- Engage with supply chain lane QATS / SQE and / OR directly with the supplier as required for implementation of permanent corrective actions
- Review status of Supplier Clinics – FIRST AID action, Root Cause and Corrective action status as well as sustenance of corrective actions
- Review and Maintain a Global Red and Green Channel list for Supplier parts and Suppliers and ensure Green to RED and RED to GREEN channel transfers happen
- Liason between CSM Engg, Dev Engg , GSC QATS , GSC SQE and Supplier for Supplier quality issues that require Cross
- Conduct Supplier PQ for Spare parts only suppliers working closely with Purchase, Buyers and Lane QATS and manage Supplier Spare parts packaging
- For Spare parts only suppliers – conduct supplier product quality (AIAG PPAP ) for parts supplied to Spare parts ONLY and /OR from Spare parts only Suppliers.
- Complete Supplier packaging approval (Packaging Data Sheet) sign off as per Spare parts needs for delivery to end customer
- Support and work closely with Lane QATS and SQE for spare parts packaging from suppliers – based on defects history and potential damages on spares due to handling / storage etc.
- Supplier Claims management and resolution to get the defect contained at source, get replacements, follow up for NC closure
- Ensure all supplier claims at Global Spare parts locations are actioned – to get the parts replacement / rework completed by suppliers working with Buyer and GSC teams
- For all containment request for Global Spare parts – work closely with Clinic Doctors, Buyer and GSC – to ensure warehouse containment stock is cleared with 7 working days – either return to supplier / rework by supplier / local rework etc ..
- Ensure all RMA returns from customers are returned back to supplier ( if defect is manufacturing or supplier issues ) OR reworked by supplier working closely with repair team .
- For parts returned by customers (RMA) – for defective cases – as required be able to do preliminary investigation in Local warehouse and also work with local material test labs / inspection labs for generating preliminary inspection reports of failed parts
- Monitor Quarantine inventory across all Global Spare parts warehouse and ensure Inventory Aging in Quarantine inventory in below 7 days
- Monitor and Reduce Quarantine disposition $ value as “SCRAP at Husky Cost “
- Ensure Supplier Non Conformance is raised (as required for few warehouse locations ) / reviewed and resolved – for Supplier spare parts claims
- Liaison with GSC lane SQE & QATS for SPP Supplier defects
- Analysis of Supplier claims – due to Customer Complaints as well as Internal receiving / shipping controls at Husky Global spare parts warehouse location
- Analysis of supplier compliant and drive systemic corrective actions working closely with the Lane QATS and SQE
- Publish the supplier claims analysis reports – by warehouse / region / supplier / lanes – with clear action plan and responsibility
- Develop a MS teams SharePoint / Business Objects reports – that is accessible for all stakeholders
- Daily reporting – by warehouse – new Supplier NC created, Status of Open Supplier NC, Clinic Updates, Quarantine inventory ($ and Aging ) by Global warehouse locations
- Prepare inspection reports – for customer specific requirement for Supplier parts – get supplier / Inhouse inspection reports to service customer order
- Create Supplier Non-Conformance report (Internal Husky factory and External Suppliers – both)
- Part manufacturing defect / dimensional issue etc. and share with SPP Quality for Supplier communication of NC. – Use template to report NC with pictures and data.
- Part count discrepancy / wrong part shipped / Visual defects – update NC report with part and shipment traceability information and relevant pictures of Nonconformance.
- Same day issue reporting and communication is mandatory.
- Communicate – daily mandatory communication
- Inspection reports – @ Receiving Controls
- Non-Conformance reports – any supplier or WT NC observed @ Japan YTC
- Maintain Sales order tracker – SO received, inspected (OK /NOK), Packed, shipped; Daily summary communicate to stakeholders
- Weekly and Monthly reports – for ANDON Clinic, Quarantine Inventory, Supplier NC status, Supplier COPQ recovery – by warehouse and Sub Territory
- Create and maintain Spare parts clinic documentation for Supplier Issues (Internal and External)
- Hands on Experience of new Supplier set up and supplier AIAG PPAP process is required; Experience of Supplier product qualification as per AIAG norms and experience of the VDA tools is added advantage.
- Hands on experience of Quality inspection (Visual and dimensional inspection) of machinery and heavy engineering machine spares- is mandatory; any associated quality inspector certification is added benefit; Should have experience using basic to complex inspection equipment like CMM, Contractor, Hardness Tester, Roughness tester and basic knowledge of metallurgy and material analysis (metal and plastics)
- Hands on experience for conducting independently / participate as team in Root Cause Analysis – is required; Use of tools like 5Why analysis, G8D, 7 Step RCA, Fish Bone Diagram – is needed
- English communication (Read / Write / Speak) – is needed, Job involves significant cross functional and cross-country communication with English as medium of communication
- Engineering education background – BE (Mech.) + Quality Certification (like Certified Quality Engr / ISO /TS Internal Auditor etc.) and Six Sigma Green Belt is an added benefit
- English Read Write Speak skill is mandatory \
- Job requires knowledge parts quality inspection – visual and dimensional – to be able to work with suppliers and engineering teams for supplier quality issues and challenges
- Read and understand Engineering drawings (Mechanical & Electrical) and Engineering Bill of Material and ability to use drawing for dimensional inspection using basic inspection tools like vernier, Micrometer, height gauge, Dial Gauge, Bore Dial Gauge
- Conduct Root cause analysis (5W/ G8D/ 7 step) with Cross functional teams
- Knowledge on Husky machines and tooling product and preferably Husky Service / Quality / Supplier Quality experience – is added advantage.
- Basic / advanced knowledge of Microsoft excel and basic knowledge of ERP (BAAN LN/ SAP / Oracle ERP etc..) – for operational needs is needed.
- Minimum 8 – 10 yrs in supplier quality and / or manufacturing process quality in similar manufacturing industry / heavy machinery / Automotive – is mandatory. Prior experience of Supplier quality is needed for this role.
- Note 1 – Role is Based out of Chennai Warehouse / Chennai MWC Office; Will require travel to supplier domestic and international as needed.
- Note 2 – Position will require parts handling / lifting / unpack and repack of machine spare parts; Packages intended for hand lifting will not exceed a gross weight of 20 Kg (44 lbs). Packages which exceed this gross limit must be handled on load carriers (pallets, skids) specifically designed for mechanical lifting devices and need to use for parts handling as a part of the Inspection and packaging task associated with the role by the Quality Inspector.
Husky TechnologiesTM offers a competitive compensation and benefits package and excellent opportunities for growth and advancement. We are committed to equal employment opportunity and respect, value and welcome diversity in our workplace. Husky TechnologiesTM also values being a great place to work and strives to maintain a safe workplace. Accordingly, Husky TechnologiesTM conditions all offers of employment on satisfactory completion of background checks. No agency or telephone inquiries please.
Husky Technologies
Stay alert for possible recruitment fraud! This can include fake websites, fake job offers, or contact from a person falsely claiming to represent Supply Chain India Jobs. Remember, neither Supply Chain India Jobs nor our representatives will ever request money from a job candidate.
If you suspect recruitment fraud and Supply Chain India Jobs is mentioned, first get in touch with our team at Supply Chain India Jobs.
Contact – info@supplychainindiajobs.com
-
Vijay SalesFull TimeMumbai, Maharashtra, India
Supply Chain Exec -
HoneywellFull TimeBengaluru, Karnataka, India
Logistics Analyst -
Peptech Biosciences Ltd.Full TimeBhiwadi, Rajasthan, India
Manager – Plant -
Dai-ichi KarkariaFull TimeMumbai, Maharashtra, India
Senior Manager -
DP WorldFull TimeUttar Pradesh, India
Executive - Hub O -
Enphase EnergyFull TimeBengaluru, Karnataka, India
Analyst_Sourcing -
DiageoFull TimeKolkata, West Bengal, India
Senior Executive- -
Trane TechnologiesFull TimeBengaluru, Karnataka, India
Operations Soluti -
NovartisFull TimeHyderabad, Telangana, India
Clinical Trial Su -
ARK IndiaFull TimeHyderabad, Telangana, India
Operations Manage -
Mahindra & Mahindra LtdFull TimeMohali, Punjab, India
Assistant Manager -
Tangar Ship ManagementFull TimeNavi Mumbai, Maharashtra, India
PURCHASE EXECUTIV -
ExxonMobilFull TimeBengaluru, Karnataka, India
Supply Planner-Ca -
EcolabFull TimePune, Maharashtra, India
Logistics Special -
AmartexFull TimePanchkula, Haryana, India
Senior Executive -
StorekaroFull TimePune, Maharashtra, India
Manager Operation -
Abbott LaboratoriesFull TimeJhagadia, Gujarat, India
Associate Directo -
MKS Industrial SolutionsFull TimeHaryana, India
Purchase Manager -
ExxonMobilFull TimeBengaluru, Karnataka, India
Vessel Logistics -
Maruti Suzuki India LtdFull TimeGurugram, Haryana, India
AM/DM - Logistics -
West Pharmaceutical ServicesFull TimeAndhra Pradesh, India
Business Support, -
Kraft Heinz CompanyFull TimeAhmedabad, Gujarat, India
Sr. Manager Globa -
OracleFull TimeHyderabad, Telangana, India
Materials Planner -
Vodafone IdeaFull TimePune, Maharashtra, India
Manager_SLS UC Op -
Beiersdorf India Serv.Priv.LimFull TimeMumbai, Maharashtra, India
Procurement Admini -
GenpactFull TimeNoida, Uttar Pradesh. India
AM - Procurement -
ALSTOMFull TimeBengaluru, Karnataka, India
SC2 Material Plan -
General MillsFull TimePowai, Mumbai, Maharashtra, India • Hybrid work
Manager, GIC Proj -
GE Aerospace (part of GE)Full TimePune, Maharashtra, India
Lead Sourcing Spe -
AppleFull TimeBengaluru, Karnataka, India
Raw Material Glob -
Baxter PlanningFull TimeIndia - Remote
Supply Chain Plann -
BungeFull TimeKandla, Gujarat, India
Executive- Logisti -
ContinentalFull TimeKalyani, West Bengal, India
Supply Chain Mana -
AmexFull TimeGurugram, Haryana, India
Operations Suppor -
ExxonMobilFull TimeBengaluru, Karnataka, India
Demand Planner - -
MeeshoFull TimeBengaluru, Karnataka, India
Associate (Cost O -
CommScopeFull TimeVerna, Goa, India
Manager, Logistic -
NinjacartFull TimeMumbai, Maharashtra, India
Procurement Team -
SolenisFull TimeBhiwandi, Maharashtra, India
Lead - Warehousin -
EstuateFull TimeIndia
Oracle SCM Functi