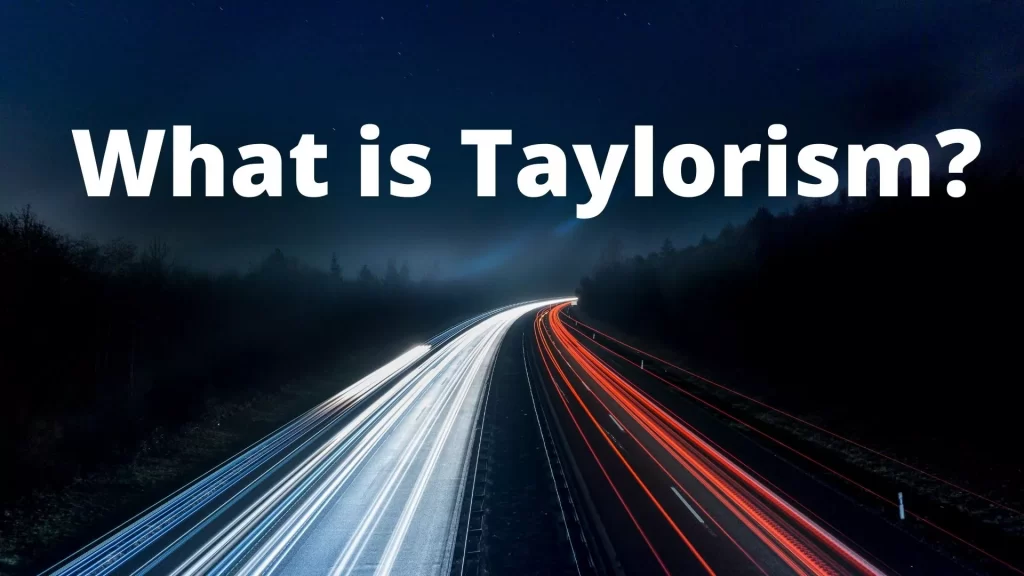
Frederick Winslow Taylor, an American mechanical engineer, started his career as a foreman at Midvale Steel Work in Philadelphia. He believed that increased productivity depends on finding ways to make workers more productive using objective and scientific techniques. Taylor devised a method for organizing labour activity based on workers’ expertise, control of time devoted to each activity, and division of tasks. In 1911, Taylor published his monograph – Principles of Scientific Management. In this article, we will learn what is taylorism and its principles.
What is Taylorism and its principles?
See Also :
- Procurement Price Tracker that can monitor 4.3 billion prices
- History and Possible Forms Of Transportation
- How Chat GPT Can Be Used To Optimize Supply Chain Management
- Refrigerated trucks – All you need to know
- What is Digital Supply Chain Management?
- What Does A Supply Chain Analyst Do?
- Career In Supply Chain Management
- What are the KPIs for E-commerce?
- What Is Indirect Procurement?
What is Taylorism?
Taylorism refers to the organization of activities in the workplace with the aim of maximizing productivity. It is often defined as a scientific or rational system of organization of work tasks that depends on mechanization to increase efficiency.
Taylor believed that flaws in a given work process can be scientifically solved through improved management methods and that the best way to increase worker productivity is to optimize the way he works.
Taylor used time-and-motion studies to analyze work steps, monitoring techniques, and worker fatigue. A time-and-action study involves identifying and measuring worker actions while performing a job and analyzing the results from those measurements. Operations that slow down the production process will be minimized. One of the goals of time-and-motion research is to design a task that is efficient and cyclical (repetitive). The elimination of wasteful body movements during labor and specifying the exact results of activities has reduced the time, money and other wastes required to create the product. He believes that the manager’s task is to determine the working methods and standards of work, and to provide workers with incentives with benefits to increase their productivity.
What does Taylorism do?
What Taylorism does is to divide the work into different rows and record the time spent by each. Each worker works in an array:
i.e. it doesn’t deal with the different steps involved in the job. Therefore, it specializes in a single stage of the production process.
Such a complex process is broken down into a few simple tasks. Each worker’s job is timed to minimize wasted time. Taylorism also makes the employee work faster based on pay for productivity.
Taylorism teachings emphasize that it has brought about a significant amount of change in industry. This Feature brought modifications like these:
It has enabled the specialization of employees, thereby increasing their skills and thus their contribution to the production and profit of the company in question.
- Give the opportunity to have more control over the work done at the different operators’ facilities.
- Thanks to the basic division of labour, it has been possible to reduce costs and reorganize things better.
What are the four Principles of Scientific Management?
Taylor’s management thought is reflected in two works “Shop Management” (1903) and “Principles of scientific Management” (1911) and summarized in 4 basic points:
>>The discovery through the scientific method of the basic elements of human work instead of relying on experience, applying the scientific working method to replace the old rules of operation.
>>Determine the planning function of the manager, instead of letting workers choose their own working method.
>>Select and train workers scientifically and develop a spirit of cooperation, rather than encouraging individual efforts and pay by piece.
>>Divide the work between the administrator and the workers so that each party does the best work for them, thereby increasing efficiency.
What according to Taylor can make employees work to their full potential?
Taylor believed that money is the answer to this question. He supported the system of individual work contracts (norms) as a basis for salary payment. If workers meet the standard, they will receive wages according to that norm. Workers who exceed the norm will receive a higher unit price for all the details of the work done, not just for the excess.
Taylorism and Fordism
Taylorism is also associated with Fordism, which is based on mass production and the use of the assembly line. The idea is that the worker should not be moving to perform his task, but that the parts should arrive at him with a machine that allows production to evolve continuously.
In Fordism, Taylorism, we should consider that a number of notable changes occurred, such as:
- Provided the opportunity to have lower prices for products when they reach the market.
- Allowed to acquire a larger capacity for profit.
Taylorism vs Fordism: What’s the Difference?
Fordism describes a method of mass production using assembly line technology invented in the early twentieth century by mechanical engineer and Ford Motor Company founder Henry Ford. Frederick Taylor actually coined the term Fordism when he accused Ford of removing the pride that humans had taken their jobs and creating a workforce of unskilled workers who were mere cars. gears in the machine. It is often assumed that Taylorism was the starting point for the manufacturing processes developed by Ford, but it is more likely that any influence on Ford from Taylorism was largely coincidental.
Popular Post :
- How to Write a Supply Chain Resume Objective in 4 Steps
- Supply Chain Manager Interview questions and answers
- Are you ready to apply if you find your dream job today?
- What is Just in Time manufacturing (JIT)?
- Phrases To Sound More Confident In Interviews
- Procurement Price Tracker that can monitor 4.3 billion prices
- Nailing Your Niche
- Select A Career Based On Your Zodiac And Supporting Planets
- 12 Important Interview Questions to Prepare for Campus Placements
- Power of AI in Optimizing Supply Chain Operations